impra®lan – the professional industrial surface coating system for timber
impralan® is the water-based complete system for industrial surface coating of wood.
Our products are specially designed to suit the highly technological needs and requirements of timber in modern industrial coating applications.
Whether the application is the industrial coating of windows, balconies, fences or cladding: the demands and requirements of the products are high. The goals are to provide the best possible quality of the products, a high level of readiness for delivery and short response times as well as comprehensive and competent service on site.
Our experts are highly knowledgeable in these areas. Furthermore, our customers have access to and can benefit from, the Impra know-how; for example our knowledge concerning impregnation of timber with inorganic compounds. We combine protection and elegant appearance and provide economically sustainable solutions to our customers.
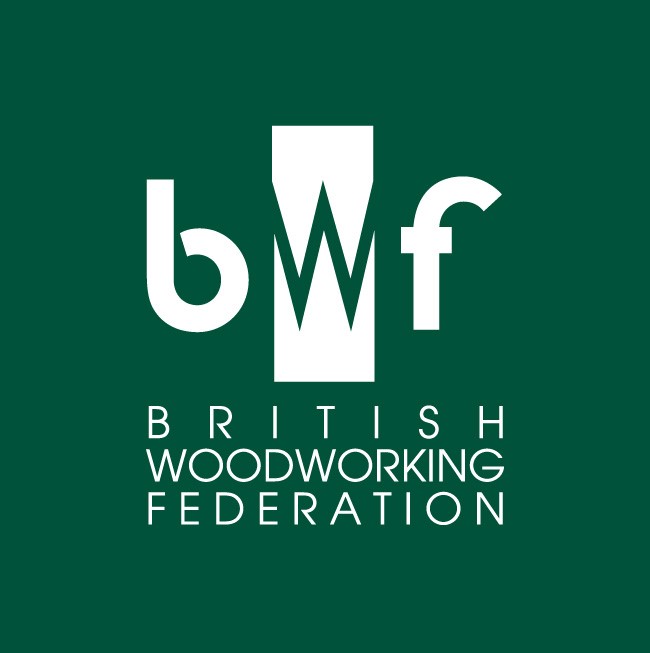
Personal on-site service
Our entire Team, including the sales force, our application engineers and research and development department is focused on providing you with the best possible solution to suit your needs and requirements.
Supply chain
The fast and reliable delivery of our products is ensured by our own extensive production and logistical locations.
Service
Whether the application is for a multi-storey timber building, coating formwork elements or landscape/garden timbers: our experienced experts are at your side to provide assistance and give technical on-site support when required.
Your benefit
- impra®lan – is a high-performance water based surface coating system specially designed for use on timber.
- impra®lan – offers an extensive product portfolio to suit various applications.
- impra®lan – combines elegant appearance with optimised timber protection; utilising our know-how and experience with biocides
Applications
Airless spraying
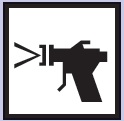
Airless is an airless atomising paint spraying process in which, in contrast to air atomisation (Airmix), the material is atomised solely via the material pressure. In this process, the material is pressurised by an electrically or pneumatically operated pump and presses the material through a nozzle bore at up to 250 bar. There, the material is split into a spray jet.
Airmix process
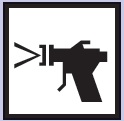
In the Airmix process, the additional air is fed into the spray jet via the nozzle slope before the paint emerges. This guarantees a quiet, stable spray jet and uniform paint application. This means that lower pressures are required.
Flooding
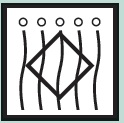
Rational, material-saving application process for primers and intermediate coatings. In special flooding systems, wooden components are sprayed with excess by means of conveyor systems, primarily in closed circuits.
Dipping
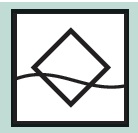
Particularly rational application method for primers and intermediate coatings, which is almost loss-free due to special dipping tubs, with usually manual handling of the individual wooden components.
Vakumat
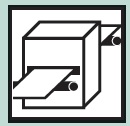
Loss- and overspray-free, profile-independent vacuum coating of profile elements and surfaces. Excess paint is applied in a housing that is closed on all sides, and is evenly extracted again by generating a vacuum. A variety of coating media and layer thicknesses can be used by changing the suction strength. Precise all-round and segmental coating is possible in a single operation. High-quality surfaces are achieved. Depending on the coating system, layer thicknesses of 10 to 200 µ/m² can be achieved. Extremely high production speeds can also be achieved.
Brush
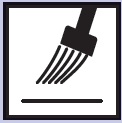
This simplest form of protective treatment is mainly used by do-it-yourselfers. In the commercial sector, the painting method is only considered in special cases due to the cost and time involved, such as the treatment of large components (e.g. glulam) or the post-protection of fresh interfaces. In order to achieve the required application quantities, several work steps are usually necessary.
ESTA
In electrostatically assisted coating, atomisation takes place via the airmix or airless process. In addition, there is a repulsion effect due to the same-pole charging of the material droplets, which can considerably refine the spray pattern. The charged droplets try to discharge themselves on a grounded object. This creates an attractive force of the droplets to the grounded workpiece. According to the ratio of attraction effect and droplet acceleration, the application efficiency can be significantly improved by this technique. Under ideal conditions, an application efficiency of up to 90 % can be achieved.